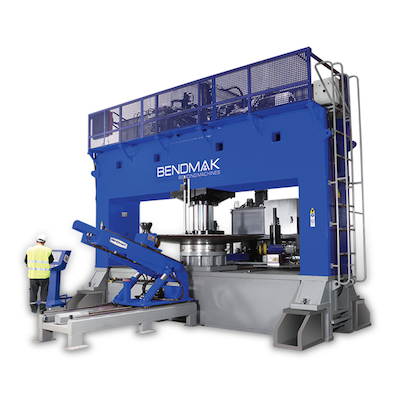
Posted By: Bendmak | Posted On: Dec 20, 2022 12:00:00 AM
Metal Fabrication: Ultimate Buyer’s Guide to Plasma Cutting Machines
CNC Plasma cutting has quickly become one of the most important and efficient methods in fabrication shops to produce shops in plate and sheet steel. Usually working opposite a laser cutting machine or Abrasive waterjet cutting systems a CNC Plasma Cutting Machine is a fast and accurate way to cut the material into near-net shapes. This guide will provide some insight as to what you should look for when buying a plasma cutting system new or used and
You will need to determine a whole lot more than just a budget when purchasing a CNC Plasma Table. You will need to consider the material you are cutting booth in type, sheet size, and thickness as well as what part accuracy is needed when finished.
CNC Plasma: Determining Your Table Size & Type
A plasma table size is first off not necessarily the size of parts you will be cutting, nor is it simply the sheet size you will be cutting your parts from. As power sources increase in capability they also become higher powered vastly increasing the cutting capacity and thus, the length of time the material takes to cool to acceptable handling temperatures. Further, the cost of extending the table is minuscule as compared to the overall cost of the system thereby allowing for staging, prep, and even post plasma work area on the tables themselves. So not only does a table have to be chosen for the work envelope of the plasma itself, but also should also be considered for a cooling zone, staging or load/unload area thus you may consider the option of doubling the length of your machine in order to have a cooling down area as well as the capability to load & unload the machine wheel it is continuing to cut.
Plasma Table Type
There are two main types of plasma tables available, wet or dry. Wet tables are typically found in the very large table sizes (12’ Cross and 40’+ length) but often are considered in smaller machines due to their initial investment cost. The advantages and disadvantages of these table types are outlined below so although it is tempting to jump on the lowest cost option, the cleanup and post cutting prep may simply not be worth it.
Water Tables
Water Tables are easily chosen as the cheapest option and they do have that advantage however material quickly cools and reforms to the parent cut material resulting in more slag and this, much more part cleanup post plasma.
Water Table Advantages:
- Price
Water Table Disadvantages
- Cleanup
- Part Rusting
- Rancid Water Smell
- Tank Cleanout
- Small Part Retrieval When Lost in Tank
- Cannot be used (submerged) with Oxy-Fuel Cutting Capabilities
Dry Tables
Dry Cutting tables come in a few different forms and can be as simple as a set of steel sawhorses supporting the plate to a steel slatted table that includes ducted and downdraft vents exhausting cutting fumes down through the table itself. These systems require a system of ducting exhaust fumes away from the cutting zone and most often, are equipped with a dust collector.
Advantages
- Cleaner Shop Environment
- Can be used with Oxy-Fuel Cutting
- Part Cleanup Is Less
- Part Retrieval is Easier
- Cleaner Shop Environment
Disadvantage
- Price
CNC Plasma Power Source - Cutting Part Accuracy
Once the overall machine size is determined the next step is determining not only the type of plasma torch(es) needed, but also their power. Next you will need to determine how many plasma torches will suffice for your needs as often machines can be equipped with 2 or more cutting torches and a variety of other accessories including plasma engravers, print heads, dot peen and paint markers for easier post processing.
Plasma Types
There are 2 main types of plasma cutting power sources (or torches) available. They are AIR PLASMA and HI-DEFINITION PLASMA. Air Plasma is typically used in hand help and mechanized operations. It produces a quality cut in a value priced package utilizing mostly common shop air. HI-Def (Hi Definition or Fine Plasma) Plasma Systems are used solely in mechanized applications such as a CNC plasma Table and provide a much finer quality of cut
Plasma Power
Power of available plasma units is determined by the units' Amperage. Determining how much amperage you need depends on a variety of factors such as the type of material you’ll be cutting and maximum material thickness. In general a 200 AMP Power source will give you clean, dross free cutting capabilities up to 1” in Mild Steel whereas a 300AMP can provide the same up to 1.5” However there are exceptions and changes when the materials change (i.e. SS and AL). Make sure you consult the plasma power source cutting capacity chart to ensure you have the right system for your needs.
CNC Plasma - Machine Design
There are several positioning systems designs available on the market today for plasma cutting. Some of the more simple designs utilize a cantilever arm or bridge with a simple single side stepper motor drive. These are typically found on your very low cost systems and you will quickly recognize their weakness in part geometry (especially rounds) and accuracy. While these design types might not be the most repeatable or accurate they are often suitable for processing work such as signs, gates that are architecturally important yet not need be geometrically correct.
If you have however determined you need a Hi definition torch for your application you very likely will also need a dual side closed loop servo system to drive that torch accurately and smoothly. Hi Definition torches can provide not only the smoothest and straightest surfaces, but their plasma streams are the tightest providing for near laser like tolerances, if they are employed on a precise and accurate drive system.
CNC Plasma - Control Type
While many CNC Controllers are designed by the manufacturer themselves providing a unique look and feel to their machine, these systems go out of date very quickly. Whether it's a firmware based system or a software/PC based system you should consider the longevity of the machine controller you're buying as once the control can no longer be supported you may end up with a dead machine.
Using a control such as the Hypertherm EDGE you will be reassured that you will have support for many years to come from not only the machinery manufacturer but the controller maker as well. You can look forward to software updates including firmware updates and feature enhancements as well.
Summary
Choosing the right CNC Plasma system can be a complex and daunting task. Fortunately you have experts on your side at BendmakUSA to assist you in choosing the right system and options to provide years of reliable cutting operation. BendmakUSA simply has the Plasma solutions precision fabricators need and want. We look forward to your inquiry.
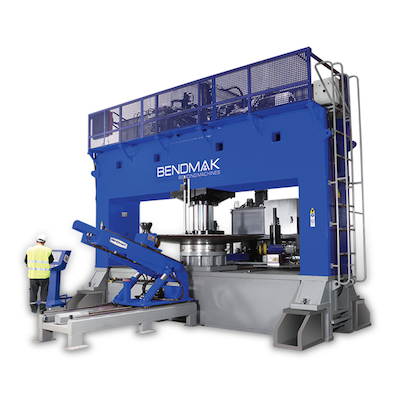