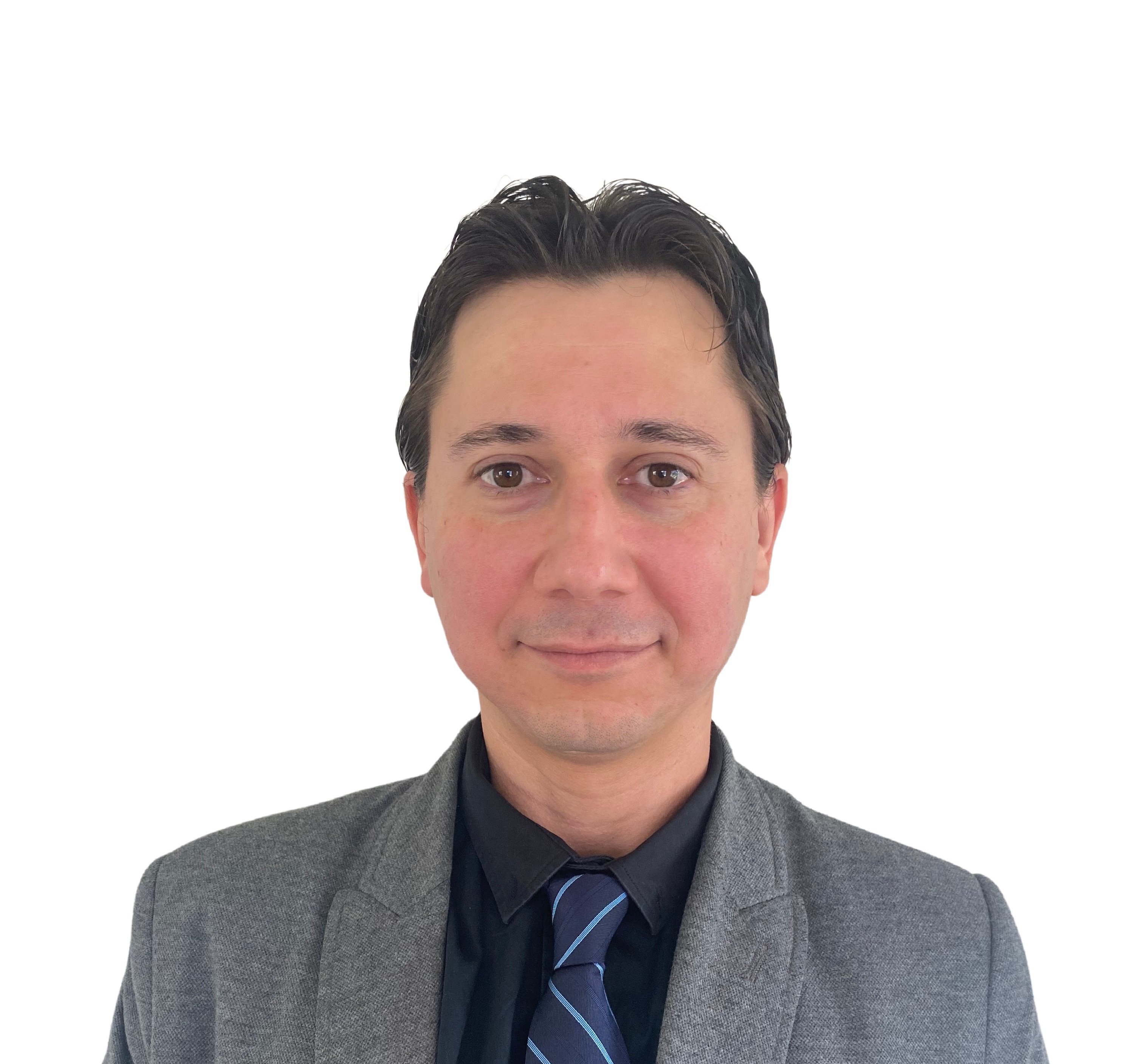
Posted By: Talip Tuzlular | Posted On: Jan 20, 2023 12:00:00 AM
Why Your Beloved Old Metal Fab Machine is Costing You a Lot of Money
As the famous Henry Ford quote suggests, “If you need a machine and don’t buy it, then you will ultimately find that you have paid for it and don’t have it.” Well, how about the old machinery you insist on keeping instead of buying new equipment?
If you’ve been relying on the same outdated manufacturing equipment for years and have stubbornly held on to it instead of upgrading to new machinery because you want to save money, you’re not alone. As it turns out, if that old machinery has been costing you more money in maintenance costs than you saved by keeping it, you’re also not alone. While it’s not uncommon to find people clinging to old equipment in hopes of saving a few bucks, it’s even more common to find that those same people end up losing more money in maintenance costs than they hoped to save.
In today’s increasingly competitive manufacturing environment, new machinery with the most modern and up-to-date technological advancements help fabricators and manufacturers produce parts with more efficiency and effectiveness with very minimal downtime. Your old machine? Maybe not as much!
How Does Metal Fabrication Machinery Get Outdated?
So how does manufacturing equipment get outdated? Just like anything else, really. Gradual improvements over the years result in machinery that is more efficient, more productive, and ultimately less costly to maintain. Holding on to old, outdated manufacturing equipment might save you some money in the short term, but it’s going to burn up your profits in the long term. No matter how you slice it, it’s just not worth it. Would you rather spend thousands of dollars a month to maintain some outdated machinery or spend a few grand on a piece of new equipment that will actually help you make more money?
How Maintenance Costs More With Outdated Equipment
Maintaining outdated equipment actually tends to cost more than maintaining newer equipment. Equipment maintenance becomes more expensive on outdated factory equipment over time. The reasons for this are multivariate. For starters, whether you like it or not, people stop producing parts for old factory equipment after that equipment has been outdated for many years. This means that when you commission maintenance or repairs on that machinery it will cost more to get the parts.
Whether you run a factory or a machine shop you'd do well to learn the pros and cons of reactive maintenance vs preventive maintenance. When it comes to reactive maintenance vs preventive maintenance, the latter beats the former in terms of cost-effectiveness every time. That’s because when you are constantly performing reactive maintenance, you’ll lose money on the downtime when the machinery is out of commission until it’s repaired.
By opting for preventive maintenance, you can keep up on repairs before the machine stops working altogether. The bottom line is, with reactive maintenance, you lose money, with preventive maintenance, you don’t lose as much money. Nothing kills profits and brings them to a screeching halt than unplanned downtime. The longer a piece of equipment is down, the more money you lose. As you might have guessed, old factory equipment tends to have more downtime than newer equipment which is another reason why maintaining outdated manufacturing equipment actually costs more than just buying new machinery.
When to Use Each Metal Fabrication Process
If you are working “Plate Steel” or “Hot Rolled” or “Pickled and Oiled” steels then a plasma cutting system is likely best suited for your needs. Generally, work processed from these materials requires only a fractional tolerance due to later forming and welding operations. Also, these materials do not perform well in laser-cutting conditions due to the surface scale. If you're working with part tolerances in the 3 decimal place range materials in Gauge thicknesses, Cold rolled steel, Stainless steel and Aluminum a laser cutting machine is likely better suited for your needs.
Check Out Our Wide New Product Lines
When it comes to buying machinery, choosing between new and used equipment is always a critical part of your purchasing decision. Now that you’ve discovered the fiscal perils of holding on to old outdated machinery you might not want to look at used equipment.
BendmakUSA is here to provide you with the most sophisticated automated manufacturing systems integrated into our large variety of new machinery product lines.
Our cutting-edge solutions range in various machinery technologies that include but are not limited to oxy-fuel plasma cutting machines, plasma-pipe profile cutting machines, CNC punching machines, heavy-duty plate drilling machines, gantry style plate processing machines, plate rolls, angle rolls, welding systems, tank turning solutions and more.
As the BendmakUSA team, we are dedicated to providing you with the best machinery solutions. To learn more about the current plasma and plate processing machines, visit bendmakusa.com.
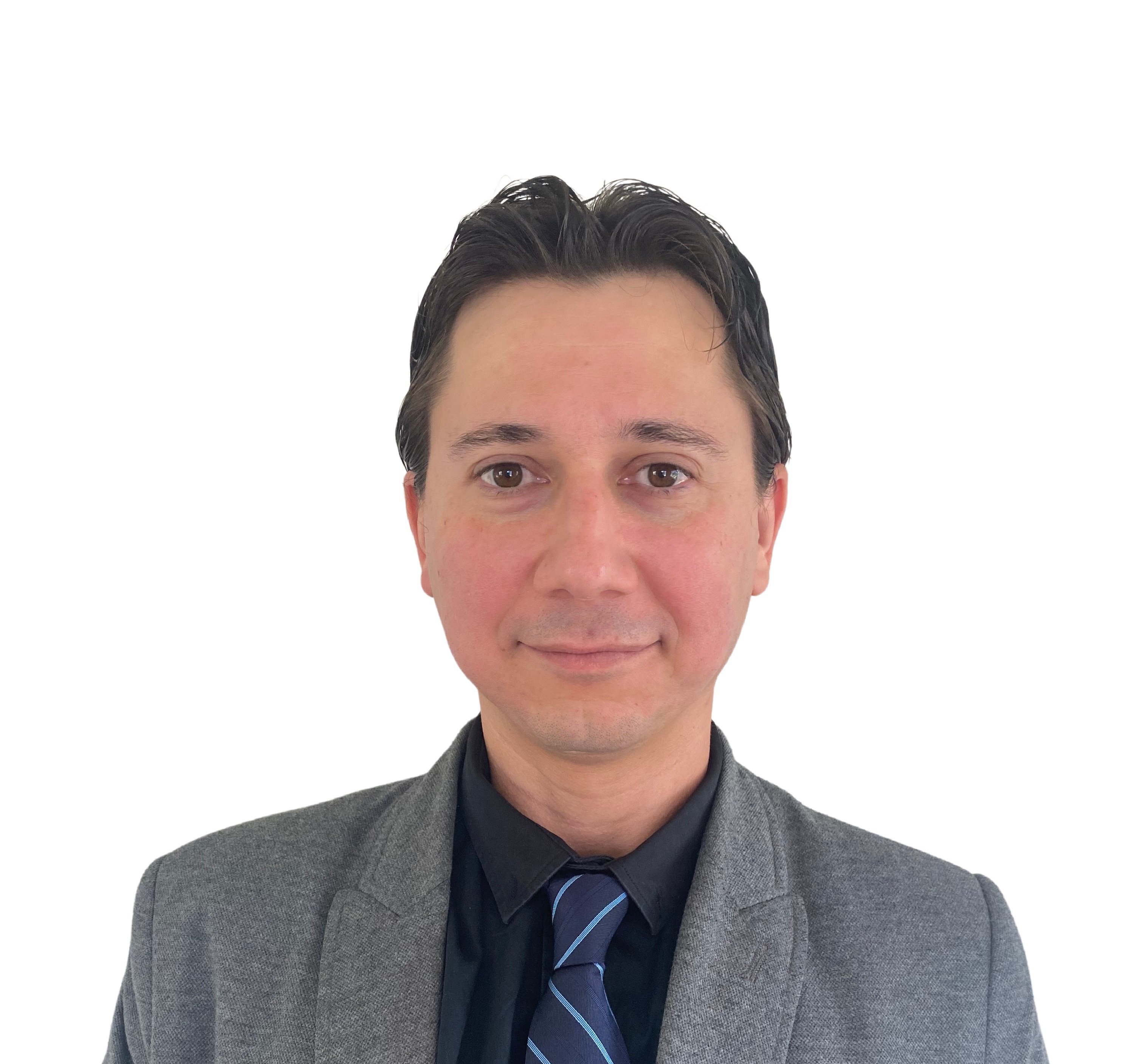