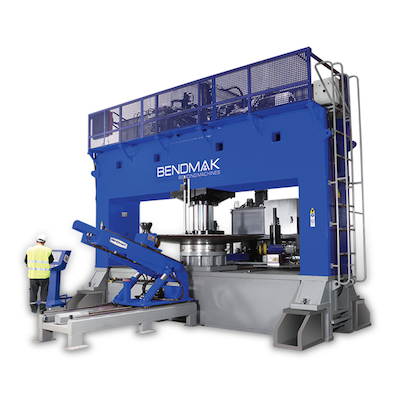
Posted By: Bendmak | Posted On: Jul 7, 2021 12:00:00 AM
Your Guide to Determining the Plate Rolling Capacity of Your Plate Roll
When searching for a plate rolling machine it is most important to first know the capacity you're looking for. Second is then to determine the style of machine best suited to your rolling needs and lastly making sure you select a quality machine builder such as Bendmak. Before we delve into the intricacies of selecting a plate roller however we should cover the basics and review machines styles and the process.
Machine Styles
There are 3 main “styles” of plate rolling machines and several variations of each. Below we have listed the miinan types of plate rolling systems available and their common uses.
- 2-Roll Plate Rolls: These types of plate rolls use a hardened upper roller and a larger diameter lower roller with a thick urethane coating. The upper roll is pressed into the lower urethane material, deforming it slightly. As both rolls turn in unison a thin piece of material is inserted between the rolls and rolled into shape. These designs of plate rolls are very application specific and used in very high production scenarios of manufacturing such as food cans.
These rolls are not commonly seen in the fabrication or job shop settings. - Initial Pinch: The initial pinch style plate roll is a 3-Roll plate roll. Often called the “slip roll”, it is one of the most common rolls found in the job shops dealing with thinner workpieces (up to 7 Gage). These rolls can be powered by manual, electronic or hydraulic action. As they are smaller they are generally easy to use but require 2 setups for pre bending the leading edge of the rolled material.
2 Rolls are set in a vertically stacked pattern and adjustable only to “pinch” the material securely. A third and adjustable roll moves at an angle toward and away from the pinching point of the first two rolls forcing the material being formed to begin to take the angle, and during rolling, the radius desired. - Variable Geometry: These style plate rolls have the roll sets in a pyramid fashion and allow for heavier bending applications in a 3 roll design. This style also allows for better cone rolling efficiency given the ability to adjust all 3 rolls however are subject to material slippage during rolling if not used correctly.
- 4-Roll: The 4-Roll plate roll design is by far the most popular as it allows rolling to be accomplished in a single setup and keeps the material clamped tightly during the entire operation. Designed with 2 rolls vertically stacked in the middle to “pinch” the material the remaining 2 rolls move laterally to prebend the leading and trailing material edges as well as force the material to the diameter desired.
Machine Rolling Process
The rolling process starts with a selected piece of material being squared up in the plate roll. In the Initial pinch and other 3-Roll machine designs this is a bit more tedious as it is a visual process. In the 4-Roll Plate roll one of the side rolls can be used as a squaring arm of sorts, to butt the material against squaring it physically before securing it between the two pinched rolls. Once the material is “pinched” securely it is adjusted until the very edge of the material is just barely past the midway or “pinch point” of the clamping rolls. Then the side roll is brought into position bending the plate to begin the angle in what is known as the pre-bend.
On 3 roll machines the material is removed, rotated and the process of pre-bending is repeated. In the 4-Roll design the material can be rolled directly from the first pre-bend until the trailing edge itself is on the opposite side roll where it then too can be pre-bent into the desired angle all whilst being firmly clamped between the 2 centered pinched rolls. Often an operator will make several “passes” to achieve the desired diameter. In some cases the operator will weld the plate ends together and attempt to “roll out” the flat ends that were created during the pre-bend process.
How to Determine Capacity
In order to determine plate rolling capacity you must first determine the hardest yielding material you will be rolling, the thickness and width of that material and the smallest diameter in which you will be rolling it to. Understand that as a certain capacity plate roll grows in plate width capability the plate rolls, by design, grow in diameter. The larger the diameter top Roll the less the diametrical capacity of the roll itself. As a rule the smallest diameter you can easily roll material down to is 1.5X the upper roll diameter (with smaller diameters achievable in multiple passes).
Capacity in a plate roll has been well engineered into the design of the machine and careful considerations must be taken most importantly with material yield strength and thickness. Consulting with your BendmakUSA representative is a quick and easy way to determine the right plate roll for your needs.
What Happens if Your Machine is Pushed Over Capacity
Often operators or fabrication shop owners will push their machines over capacity. Although all machines are designed for a range of safety above their designated range, eventually you can damage the machine, and in some cases severely. One of the first and most common issues with used plate rolling systems is bent rolls. When rolls are pushed beyond their limit over a shorter range of their surface they can be easily deformed. Another common issue when rolls are overstressed along their full capacity, is breaking of the top roll at the tapered end that fits into the drop end. This area of the top roll is weakest and can succumb easily to highly overstressed scenarios.
Selecting the right plate roll for your needs and budget is a simple process with your BendmakUSA representative. Our team has the know-how to help you select the right plate roll for your application. Call us today at 833-BENDMAK or visit us on the web at WWW.BENDMAKUSA.COM
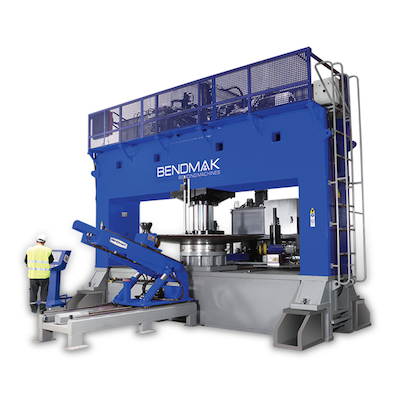