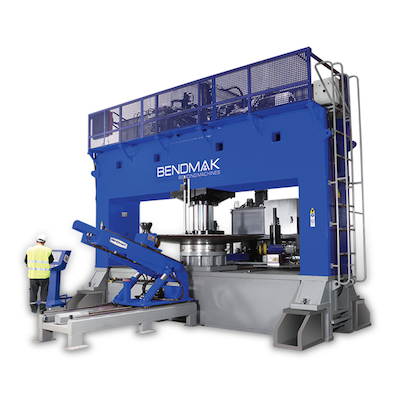
Posted By: Bendmak | Posted On: Jun 12, 2023 12:00:00 AM
Plate Rolling Techniques: Understanding The Different Methods
Plate rolling is a process that involves bending metal plates to form cylinders or curved shapes. It is a common metal fabrication technique used in various industries, including construction, aerospace, and manufacturing. Plate rolling techniques vary depending on the material being used, the thickness of the plate, and the desired shape. In this article, we discuss the different plate rolling techniques and their advantages and disadvantages.
Initial Pinch Roll Bending
Initial pinch bending is the most common plate rolling technique used in the industry. It involves feeding the metal plate through a set of three rollers, which apply pressure to the plate and bend it into a cylindrical shape. The three rollers are arranged whereas two rollers are aligned vertically and provide both the pinching (gripping) function and the rolling or feeding of the material. The third roll approaches from below and behind these pinch rolls to push the plate being formed into the radius desired.
Initial Pinch bending is a versatile design that is common in smaller material thicknesses (typically gauge materials) and can be used on a wide range of materials, including steel, aluminum, and titanium. The advantages of three-roll bending include ease of use, machine price, high precision, excellent repeatability, and the ability to produce large quantities of parts. However, it is not suitable for forming complex shapes or thicker & wider widths of materials. This forming method also requires the operator to remove the plate, rotate it 180° and reinsert it in order to pre-bend each end of the material being formed.
Four-Roll Bending
Four-Roll bending is a more advanced plate rolling technique that involves the use of four rollers instead of three. The rollers are arranged in a diamond shape, with the two smaller rollers at the sides providing the resistance against the plate being formed and the two larger rollers at the top & bottom. The plate is fed through the middle two rollers, which apply pressure to the plate constantly pinching it and providing the feeding of the plate, while the side two rollers apply pressure to the bottom of the plate in order to force it into the radius, or shape being formed.
Four-roll bending has several advantages over three-roll bending, including the ability to form complex shapes and the ability to roll thicker plates. It is also more efficient and requires less material handling than three-roll bending as it can pre-bend each end of the plate in one setup without having to remove and rotate the material. Altrhough a 4-Rolll Plate Roll is more expensive, it can save vast amounts of time when rolling and provide superior accuracy as the material is constantly pinched in the forming process. Also four roll machines are capable of rolling thinner materials all the way to materials in excess of 4" (100MM) in thicknesses.
Variable Geometry Rolling
Variable geometry rolling is a plate rolling technique that involves the use of a machine designed with 3 rolls in pyramid placement. The roller can be adjusted to form different shapes, including cones, cylinders, and elliptical shapes. The technique is suitable for a wide range of materials, including stainless steel, aluminum, and titanium, and can be used to form parts with a thickness of up to 6 inches.
Variable geometry rolling has several advantages over other plate rolling techniques, including the ability to form complex shapes and the ability to produce parts with a high degree of precision. It is also more efficient and requires less material handling than other techniques. However, it is more expensive and requires specialized equipment.
Conclusion
Plate rolling is a versatile metal fabrication technique that is used in various industries to form cylinders or curved shapes. There are several plate rolling techniques available, including Initial Pinch, Four-Roll & Variable Geometry Rolling. Each technique has its advantages and disadvantages, depending on the material being used, the thickness of the plate, and the desired shape. It is important to choose the right plate rolling technique for your application to ensure that you achieve the desired outcome. At BendmakUSA our expert staff can assist in choosing the right plate roll with the right optional accessories for your application and budget.
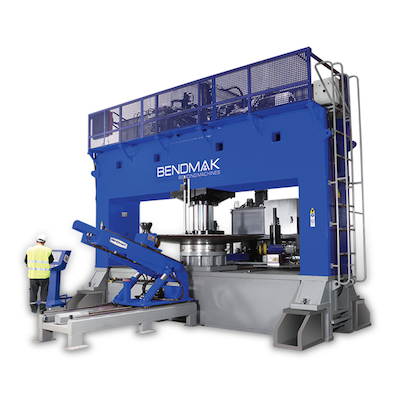