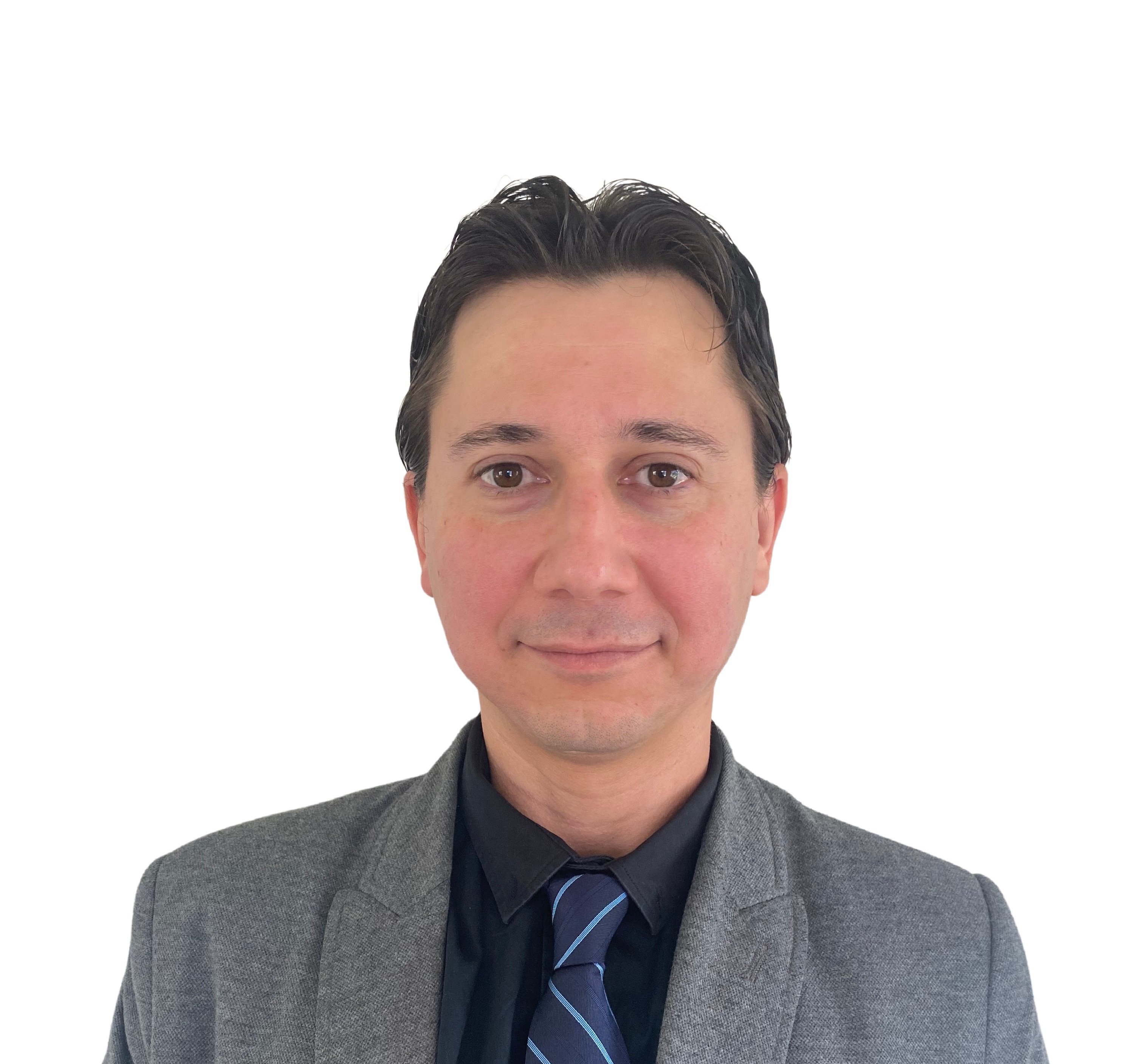
Posted By: Talip Tuzlular | Posted On: Aug 4, 2022 12:00:00 AM
Types of Sheet Metal Rolling Equipment and How They’re Used
Have you ever thought about how sheet metal is produced, classified and what kind of applications they are for? Understanding how sheet metal rolling actually works, it is important to know what sheet metal is and does. As its name suggests, sheet metal is a piece of metal formed into a thin layer of sheet. This formation is achieved through a series of rolls reducing the thickness of the metal till it becomes a sheet metal.
One thing to keep in mind is the difference between a sheet and plate. Generally speaking, plate refers to thicker flat metals and sheet refers to thinner flat metal pieces. The rule of thumb would be any thickness over ⅛” can be considered as plate and anything thinner than that would be sheet metal. Now, let’s dig into the sheet metal rolling process.
How the Sheet Metal Rolling Process Works
Sheet metal is used in a variety of applications including but not limited to ductwork, machine components, construction and so on. There are numerous types of processes that sheet metal may be formed by. Bending, laser cutting, press brake forming, water jet cutting and roll forming, just to name a few. One of the most popular and widely used methods is sheet metal rolling of flat sheet metal pieces or coiled strips that are processed through a metal sheet rolling machine. These machines are also known as “metal roller” or “metal bending roller”.
Common Types and Uses of Sheet Metal Rolling Equipment
There are many types and uses of sheet metal rolling equipment in the metal fabrication industry. Below, you will find the most common ones.
Power Slip Rollers
Power slip rollers are some of the most common and widely used sheet metal rolling machines that are available in the market. These machines typically weigh about 700-1000 lbs, have smaller motors (2hp-3hp) and work on single phase 220V. Power slip rollers are great for small cylindrical applications.
Manual Ring Rollers
These small but sturdy and powerful rollers can be great for very small formations. They can form rings as small as 1” diameter.
Sheet Metal Slip Rollers
These machines are also known as plate rollers. Plate rollers typically handle greater thickness materials and long sheet metals or plates. The typical and most common lengths range between 4’ and 10’. These machines can be manual or powered with a digital readout.
Tennsmith Slip Rollers
Tennsmith slip rollers are also known as pinch rollers. These machines look very simple but due to the precisely parallel rolls of these machines, tight and perfectly formed sheet metal can be achieved.
2-Cylinder Metal Rollers
As the name suggests, these machines have 2 cylinder rolls to form sheet metal.Typically, one of the rolls will have a larger diameter than the other one and the smaller one applies force to the material to shape. These metal rollers are fairly easy to use and great for smaller applications.
3-Cylinder Metal Rollers
The third cylinder on 3-cylinder rollers provides a significant amount of rolling power to the machine. 3-cylinder metal rollers are often used for sheet metal that is no thicker than an inch. Some robust and well-built 3-cylinder rollers may be able to handle thicker than an inch material though (depending on the sheet metal's yield point and various other factors). These types of metal bending rollers are great for mid-range size projects.
4-Cylinder Metal Rollers
4-Cylinder Metal Rollers provide a reliable and perfect solution for sensitive and demanding rolling. It is the most rational choice for bending materials with plate thickness from 14 Gauge to 8" thick with material widths from 20" to 40'. In addition to its reliability the design of these types of machines increases productivity with its high rolling speed and can easily overcome the most difficult bends thanks to their ease of use and Double Pinch design. As the plate is always pinched tight during pre-bend, rolling and post-bending, slipping of the material is eliminated. Thus, better more accurate bends are made and more precise results are obtained.
With the design of the 4-Cylinder Rolling Machines, one of the side rolls can be used as a "squaring gauge" so that the material can be easily and precisely aligned to the pinch rolls. Further, utilizing the 4-Cylinder Rolling Machine design, it is possible when pre-bending and rolling, that the material can be compressed enough with the lower shaft that it is possible to obtain a full cylinder in one pass. This unique design also allows the plate to be clamped precisely between the upper and lower rolls, thus minimizing the amount of flat ends on the formed plate.
How to Find the Best
BendmakUSA CNC 4-Cylinder Rolling Machines with superior engineering and design are some of the greatest machines available in the market.
Check out our 4-Cylinder Rolling Machines on our website for more details or call us for more information at 833-BENDMAK (833-236-3625)
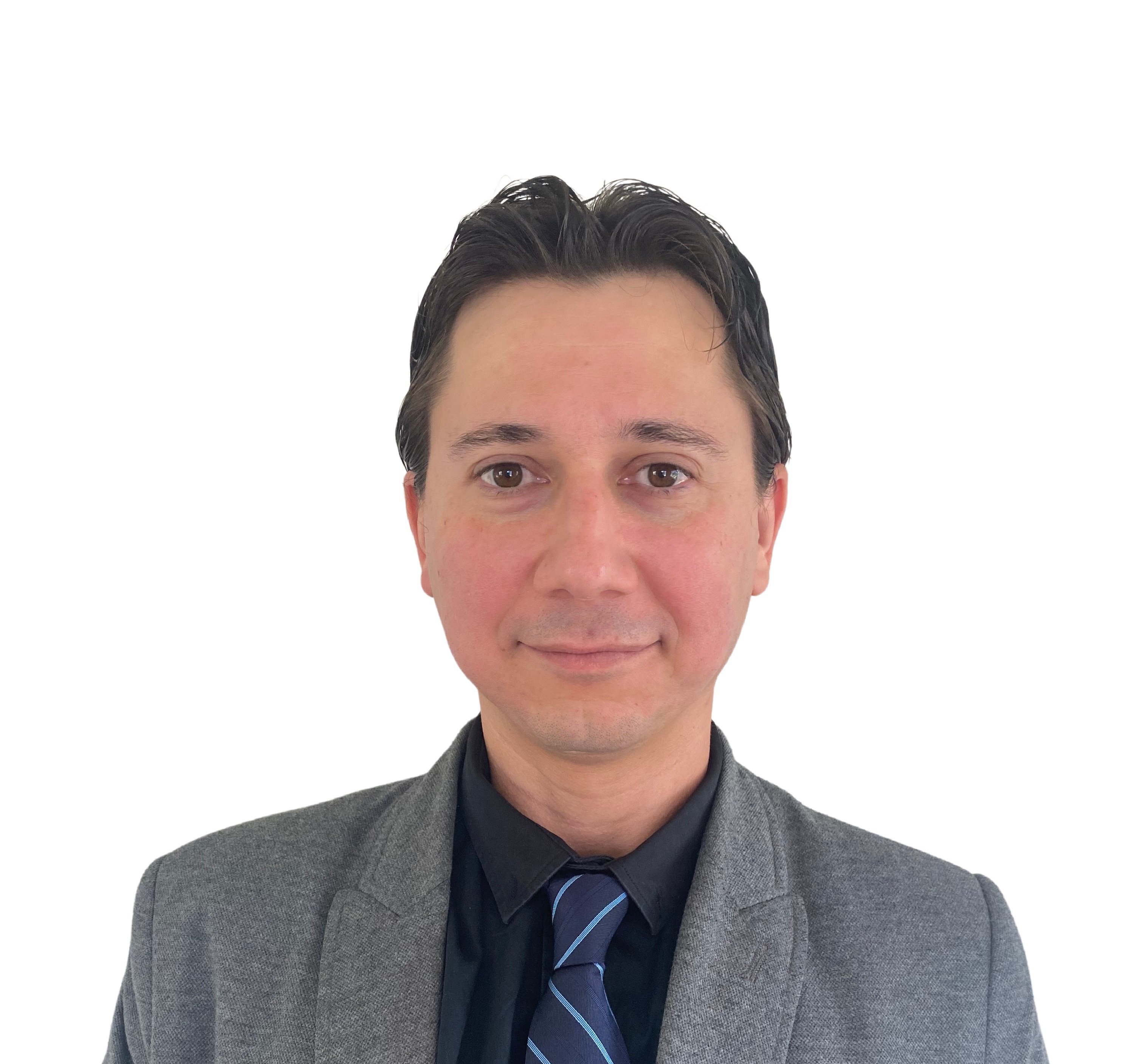