Posted By: Andrew Kamashian | Posted On: Feb 3, 2025 6:00:00 AM
BendmakUSA CR vs. SAR Tank Rotators: A Manufacturer’s Guide
BendmakUSA CR vs. SAR Tank Rotators: A Manufacturer’s Guide
9:18
Tank Turning Rolls
As a tank manufacturer, your production line’s efficiency, welding quality, and adaptability to various tank designs are critical to your success. Tank rotators are indispensable tools in this process, enabling precise rotation of cylindrical workpieces like tanks, pressure vessels, and pipes during welding and assembly. BendmakUSA offers two prominent options: Conventional (CR) Tank Rotators and Self-Adjusting (SAR) Tank Rotators. While both serve the same fundamental purpose—rotating rolled shells / tanks for fabrication—they differ significantly in design, functionality, and application. This article dives into these differences, tailored to your needs as a tank manufacturer, and uses illustrations to clarify key points.
What Are CR Tank Rotators?
BendmakUSA’s CR Tank Rotators are a conventional, robust solution designed for rotating cylindrical parts with consistent diameters. These rotators consist of two primary units: one driven (powered) unit and one idle (freewheeling) unit. The driven unit, equipped with a motor and gearbox, controls the rotation, while the idle unit supports the workpiece. Operators can adjust the wheel centers manually or via a control panel to match the tank’s diameter, ensuring stable and secure rotation.
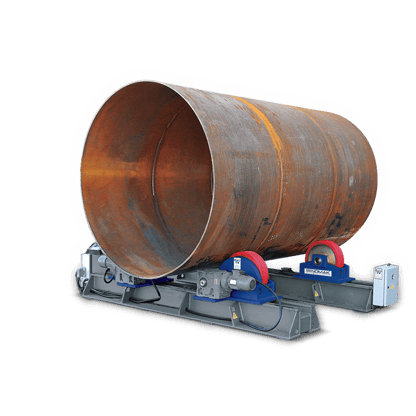
Imagine a cylindrical tank resting on two sets of rollers. The left side has a motor-driven roller (the driven unit), while the right side has a passive roller (the idle unit). The tank rotates smoothly as the driven unit powers the motion, with the operator setting the speed via a control panel. CR rotators are built for simplicity and durability, using high-quality steel and polyurethane-coated wheels to withstand heavy loads and tough conditions. BendmakUSA offers CR models ranging from 1 to 300 tons, with custom options up to 600 tons, making them suitable for a wide range of tank sizes.
What Are SAR Tank Rotators?
SAR (Self-Adjusting) Tank Rotators, also from BendmakUSA, are engineered for versatility. Unlike the CR’s fixed setup, SAR rotators feature self-aligning rollers that automatically adjust to the tank’s diameter—no manual tweaking required. This is achieved through a pivoting yoke assembly or hydraulic sensors that adapt to the workpiece’s shape as it’s loaded. Like the CR, SAR rotators include a driven and an idle unit, but their adaptability sets them apart.
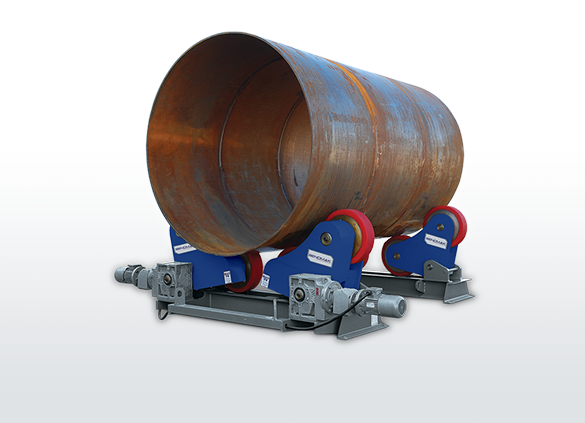
Picture a tank with an irregular oval shape placed on an SAR rotator. The rollers, mounted on adjustable arms, pivot inward or outward to hug the tank’s contour automatically. The driven unit rotates the tank, while the idle unit follows, maintaining perfect alignment without operator intervention. SAR models are ideal for tanks with variable diameters, such as ovals or thin-walled vessels, and range from 3 to 300 tons in capacity, with custom builds also up to 600 tons. They’re designed to minimize setup time and crane use, boosting workshop efficiency.
Key Differences for Tank Manufacturers
As a tank manufacturer, your choice between CR and SAR rotators hinges on your production needs. Let’s break down the differences across several critical aspects:
1. Adjustability and Setup Time
-
CR Rotators: Require manual adjustment of wheel centers to fit the tank’s diameter. This process, while straightforward, takes time—especially if you’re switching between tank sizes frequently. For example, moving from a 2-meter to a 4-meter diameter tank means repositioning the rollers and securing them, adding minutes to your workflow.
-
SAR Rotators: Automatically adjust to the tank’s diameter upon loading. This eliminates setup delays, making SAR rotators a time-saver in dynamic production environments where tank sizes vary.
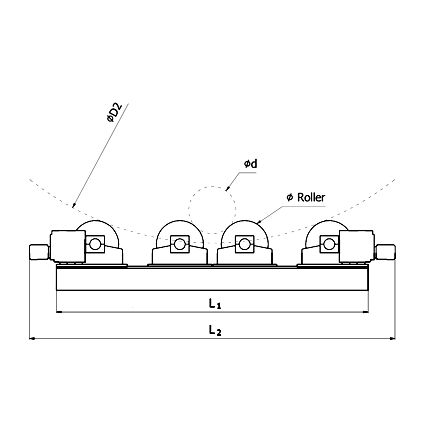
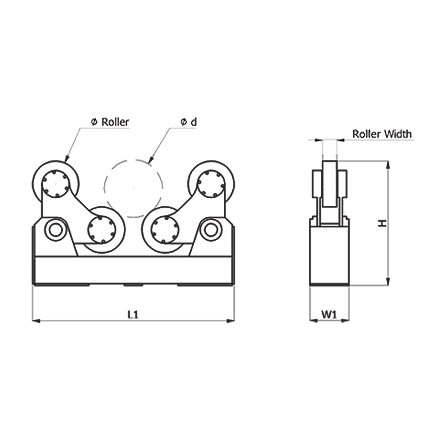
For CR: A worker adjusts the roller spacing with a wrench, aligning it to a fixed-diameter tank. For SAR: The tank is simply placed on the rollers, which shift instantly to fit, ready for rotation in seconds.
If your shop produces tanks of consistent size—say, standardized pressure vessels—CR’s manual setup is manageable. But if you handle custom orders with diverse diameters, SAR’s automation is a game-changer.
2. Application Suitability
-
CR Rotators: Excel with tanks of uniform diameter and a stiffer wall thickness. Their fixed roller design ensures stable, precise rotation for cylindrical welding, ideal for repetitive production runs like fuel tanks or pipelines. They’re less suited for irregular shapes, as manual adjustments can’t compensate for ovality or asymmetry.
-
SAR Rotators: Shine with variable-diameter or thin-walled tanks. The self-aligning rollers distribute weight evenly, reducing pressure points that could dent delicate stainless-steel vessels (e.g., up to 8mm thick). They’re perfect for custom tanks or applications like tower pipes and reactors.
CR: A perfectly round tank rotates smoothly on fixed rollers. SAR: An oval tank sits securely as the rollers pivot to match its uneven contour, preventing slippage or damage.
For high-volume, uniform tank production, CR rotators are cost-effective. For bespoke or fragile tanks, SAR rotators offer unmatched adaptability.
3. Cost and Complexity
-
CR Rotators: Simpler design translates to lower upfront costs and easier maintenance. With fewer moving parts (no self-adjusting mechanisms), they’re less prone to wear, appealing if budget and simplicity are priorities.
-
SAR Rotators: Higher initial investment due to advanced engineering (e.g., hydraulic or pivoting systems). Maintenance may require specialized attention, but the time saved in setup often offsets the cost for high-variability shops.
As a manufacturer, weigh your capital budget against production flexibility. CR suits tight margins; SAR justifies itself with efficiency gains.
4. Operator Control and Precision
-
CR Rotators: Offer precise control via a panel, with adjustable speeds and clockwise/counterclockwise rotation. This suits manual or automatic welding where consistency is key, like longitudinal seams on thick-walled tanks.
-
SAR Rotators: Match CR’s control features but add automation. The self-alignment ensures consistent roller contact, reducing “bikini weld” issues (uneven welds from speed fluctuations) on long seams—a boon for quality-focused manufacturers.
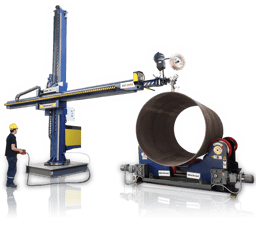
CR: A steady weld forms on a uniform tank, controlled manually. SAR: A long seam welds evenly as self-aligning rollers maintain stable rotation, avoiding width variations.
If weld integrity is your hallmark, both deliver, but SAR enhances precision with irregular tanks.
5. Load Capacity and Durability
-
CR Rotators: Built for heavy-duty use, with robust frames and wheels handling up to 600 tons in custom builds. They’re ideal for thick-walled nuclear vessels or steam generators.
-
SAR Rotators: Equally durable, with capacities up to 600 tons, but their multi-wheel design better supports thin-walled tanks by distributing load, preventing dents.
For mega-tanks, either works; for lighter, delicate ones, SAR has the edge.
Practical Implications for Your Shop
Consider your production profile:
-
High-Volume, Uniform Tanks: CR rotators are your ally. Their simplicity and lower cost align with repetitive tasks. A shop churning out 100 identical 3-meter fuel tanks daily benefits from CR’s reliability without needing SAR’s adaptability.
-
Custom, Variable Tanks: SAR rotators shine here. If a client orders a mix of 2-meter oval reactors and 5-meter cylindrical silos, SAR’s quick adaptability keeps your line moving, reducing downtime and labor.
CR: A row of identical tanks rotates on CR units, welded efficiently in sequence. SAR: A mix of tank shapes rotates seamlessly on SAR units, no adjustments needed between jobs. Safety also matters. CR’s fixed support minimizes slippage risks with uniform loads, while SAR’s auto-adjustment stabilizes irregular tanks, enhancing worker safety.
Making Your Choice
As a tank manufacturer, align your rotator choice with your workflow:
-
Choose CR Rotators If: You prioritize cost, simplicity, and uniform tank production. They’re reliable workhorses for standard jobs.
-
Choose SAR Rotators If: Flexibility, speed, and varied tank designs define your business. They’re an investment in adaptability and quality.
BendmakUSA backs both with robust engineering, offering capacities from small-scale to massive 600-ton projects. Assess your tank sizes, production pace, and budget. For a hybrid approach, some shops pair CR for bulk work with SAR for custom jobs—maximizing efficiency across the board.
BendmakUSA’s CR and SAR Tank Rotators cater to distinct needs in tank manufacturing. CR offers simplicity and precision for uniform production, while SAR delivers flexibility and speed for diverse designs. By understanding your shop’s demands—illustrated through these practical differences—you can choose the rotator that boosts your productivity, quality, and bottom line. Whether it’s the steady CR or the agile SAR, BendmakUSA equips you to weld tanks that stand the test of time.
Andrew Kamashian
Andy Kamashian has extensive experience in machining & metal fabrication. Starting as an apprentice in a machine shop and progressing into machinery sales he has worked hands on with the very same machinery, materials and processes he writes about today. Andy's knowledge is shared not only in the sales aspects at BendmakUSA, but also in the application of their machinery as well.