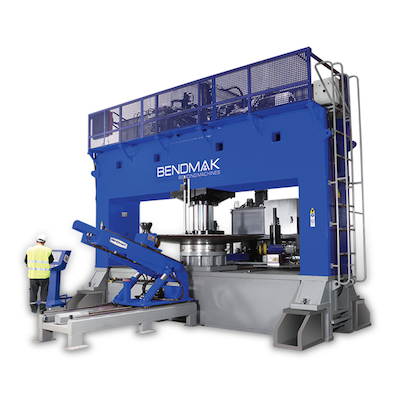
Posted By: Bendmak | Posted On: Jun 16, 2023 12:00:00 AM
What You Need to Know About Dishing & Flanging Machinery
In the fabrication of Metal Tanks there are 3 very important processes. The first is plate rolling which rolls the steel into a tube shaped structure for the main body of the tank but the lesser known processes are the dishing and flanging operations required to make the tank ends.
What is Dishing & Flanging?
Dishing and flanging are two metal forming processes that are commonly used in the manufacturing industry. Dishing is the process of forming a shallow dish or bowl shape in a piece of metal, while flanging is the process of forming a flange or lip around the edge of a piece of metal. These processes are often used in the production of metal containers, such as tanks, drums, and cans. Dishing and flanging can be done using a variety of different machines, including hydraulic presses, mechanical presses, and spinning machines (thin sheet aluminum & steel only). Each of these machines has its own advantages and disadvantages, and the choice of machine will depend on the specific requirements of the job.
The most common dishing machine is the hydraulic press which can be used to form the dome on material thicknesses from thin gages to several inches thick. On the Dishing Press the operator loads the sheet blank in and uses the press to form the dome into a bowl shape. Once that desired shape is achieved the next step is to load it onto the flanging machine which rotates the sheet while bending the edge or lip of the dome into a flange in order to be welded onto the plate rolled diameter of steel. While flanging is not always required it is typically necessary for integrity of tanks, especially those used in higher pressure applications.
Sizing a Dishing & Flanging System
When sizing a dishing and flanging system, there are several factors that need to be taken into consideration. These include the size and thickness of the metal being formed, the required shape and dimensions of the finished product, and the production volume required. The size and thickness of the metal being formed will determine the size and capacity of the dishing press and the tonnage and size of the flanging machine that is required. For example, if you are forming high pressure gas storage tanks, you will need a machine with a large capacity and a high tonnage rating.
The required shape and dimensions of the finished product will also play a role in determining the size and type of machine that is required. For example, if you are forming a shallow dish or bowl shape from very thin or easily malleable materials, you may be able to use a spinning machine, which is a type of lathe that is specifically designed for metal spinning. However, in most cases if you are forming a more complex shape, such as a pressure vessel, tank or drum, you may need to use a hydraulic or mechanical press. Finally, the production volume required will also play a role in determining the size and type of machine that is required as well as the options chosen on it. If you are producing a large volume of metal containers, you will need a machine that is capable of high-speed production and can handle continuous operation.
Shopping for the Best Dishing & Flanging Machinery
When shopping for dishing and flanging machinery, there are several factors that you should consider. These include the type of machine, the capacity and tonnage rating, the features and options available, and of course, the price. The type of machine that you choose will depend on the specific requirements of your job and production ratings. As mentioned earlier, there are several different types of machines that can be used for dishing and flanging, including hydraulic presses, mechanical presses, and spinning machines. Each of these machines has its own advantages and disadvantages, and the choice of machine will depend on the specific requirements of the job. It is best to consult with a professional dealer like BendmakUSA that understands and can recommend the right solution for your needs.
It's also very important to note that some machines may come with additional features, such as programmable controls, automatic tool changers, and safety features that could be very vital to your operation. These features can help to improve the efficiency and safety of the machine, and may be worth considering if they are within your budget. Finally, the price of the machine will also be an important consideration. Dishing and flanging machinery can be expensive, and it is important to not set budget until you have explored the designs available and discussed with an expert which machine is the right one for you, with the options needed for your application. It is also important to remember that the cheapest machine may not always be the best value, and it may be worth investing in a higher-quality machine that will last longer and require less maintenance over time such as the Bendmak Series of Dishing and flanging machines.
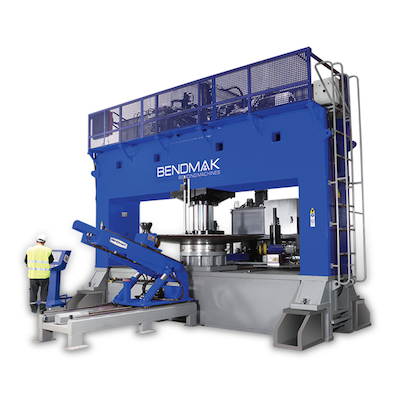