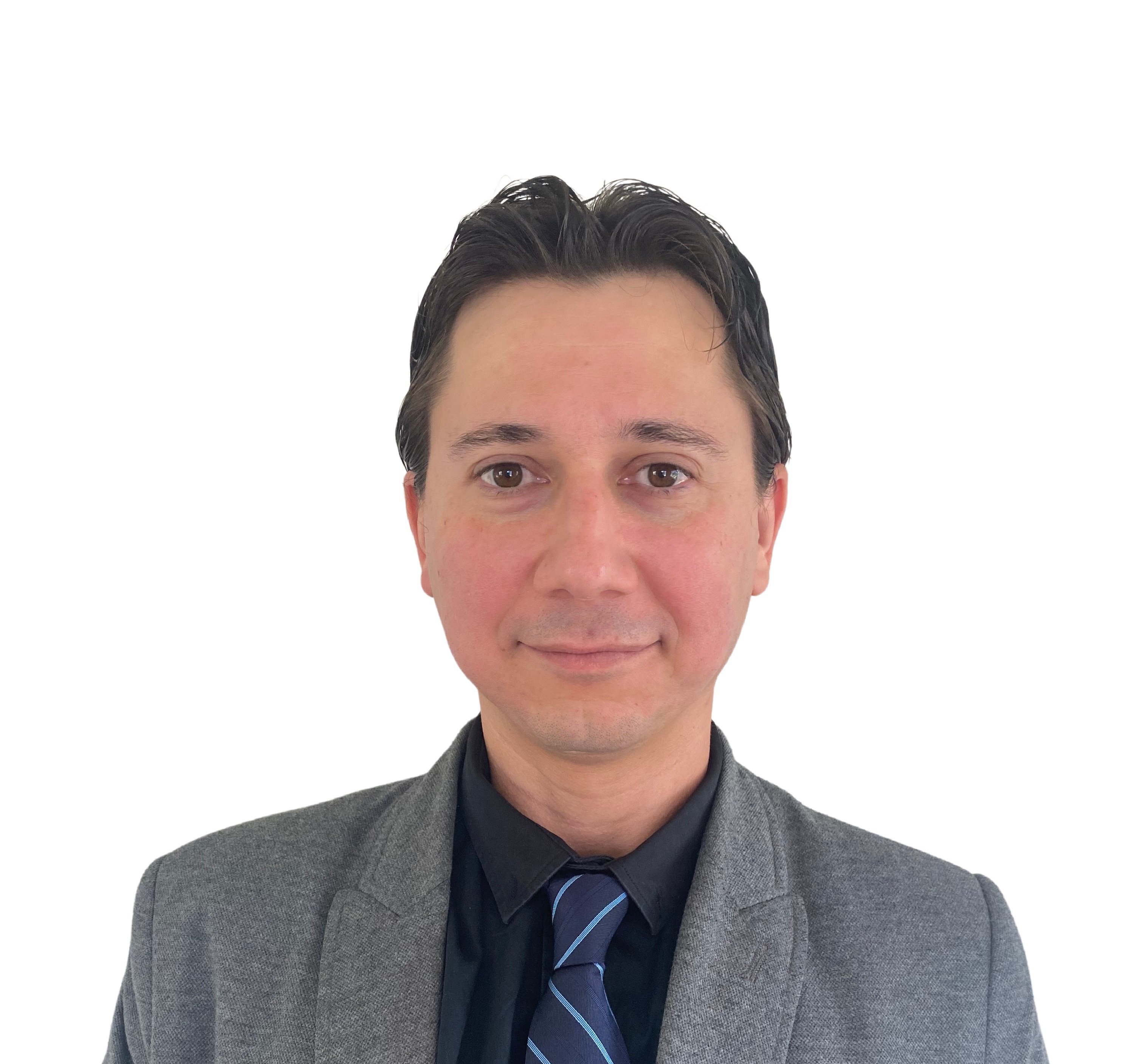
Posted By: Talip Tuzlular | Posted On: Dec 21, 2022 12:00:00 AM
Comparison Between 2 Fabrication Techniques: Plasma Cutting vs Laser Cutting
Is your machine shop or manufacturing plant looking for ways to be more efficient and increase productivity? If you answered YES, then you’ll need to learn the difference between Plasma Cutting and Laser Cutting. You will also need to know the pros and cons of each and which purposes they’re best suited for. So what’s the difference between a high-definition plasma and a laser cutting machine? What benefits do they bring?
In today’s increasingly competitive manufacturing environment, plasma and laser cutting machines help fabricators and manufacturers produce parts with more efficiency and effectiveness with very minimal downtime. The question is which one is better? You’re about to find out!
What is Plasma Cutting?
Plasma cutting is a technique that involves a power source that generates intense heat through a plasma stream. This plasma stream controlled by a CNC controller is positioned and moved over a conductive piece of material to cut, or rather burn, profiles into and out of that metal. Plasma cutting machines in general are much less expensive to purchase, and simpler to operate (more forgiving of conditions) than their counterparts, laser cutting machines.
What is Laser Cutting?
Laser cutting is a technique that uses an intense light source to produce heat and like the plasma cutting machine is controlled by a CNC Motion controller to move the cutting head over materials to burn, or vaporize the material away. Unlike the plasma cutting system the laser machine does not need the material to be conductive but due to the small size of the beam is more limited in material thicknesses. The cutting laser is prized for its precision, accuracy, speed, and overall efficiency in thinner materials.
A high-quality laser cutting machine makes it also possible to cut and etch simultaneously which greatly improves workflow and speeds up the production process. Machine shops using laser cutting machines can easily outperform less progressive outfits that rely solely on plasma cutting equipment, provided the materials fall within the range of acceptability for their laser capacity. If a shop is working with very precise fabricated components in gauge material thicknesses and laser cutting system is the right choice.
When to Use Each Metal Fabrication Process
If you are working “Plate Steel” or “Hot Rolled” or “Pickled and Oiled” steels then likely a plasma cutting system is best suited for your needs. Generally, work processed from these materials requires only a fractional tolerance due to latter forming and welding operations. Also, these materials do not perform well in laser-cutting conditions due to the surface scale.
If you're working with part tolerances in the 3 decimal place range materials in Gauge thicknesses, Cold rolled steel, Stainless steel, and Aluminum a laser cutting machine is likely better suited for your needs.
The Advantages of Plasma Cutters Over Laser Cutters
The primary advantage that laser cutting has over a plasma cutting system is speed, precision, and accuracy in thinner gauge materials. The plasma cutting system has its applications as plate thicknesses increase providing speed & accuracy & an even better value.
Remember, time is money which means that anything that can help you save time will help you save money as well. If you need a lot of thicker and rougher work made plasma is your best option.
How Can We Help?
BendmakUSA is here to provide you with the most sophisticated automated manufacturing systems integrated into our plasma cutting machines.
Our cutting-edge solutions range in various machinery technologies that include but are not limited to oxy-fuel plasma cutting machines, plasma-pipe profile cutting machines, CNC punching machines, heavy-duty plate drilling machines, gantry style plate processing machines, and more.
As the BendmakUSA team, we are dedicated to providing you with the best machinery solutions. To learn more about the current plasma and plate processing machines, check out our website bendmakusa.com
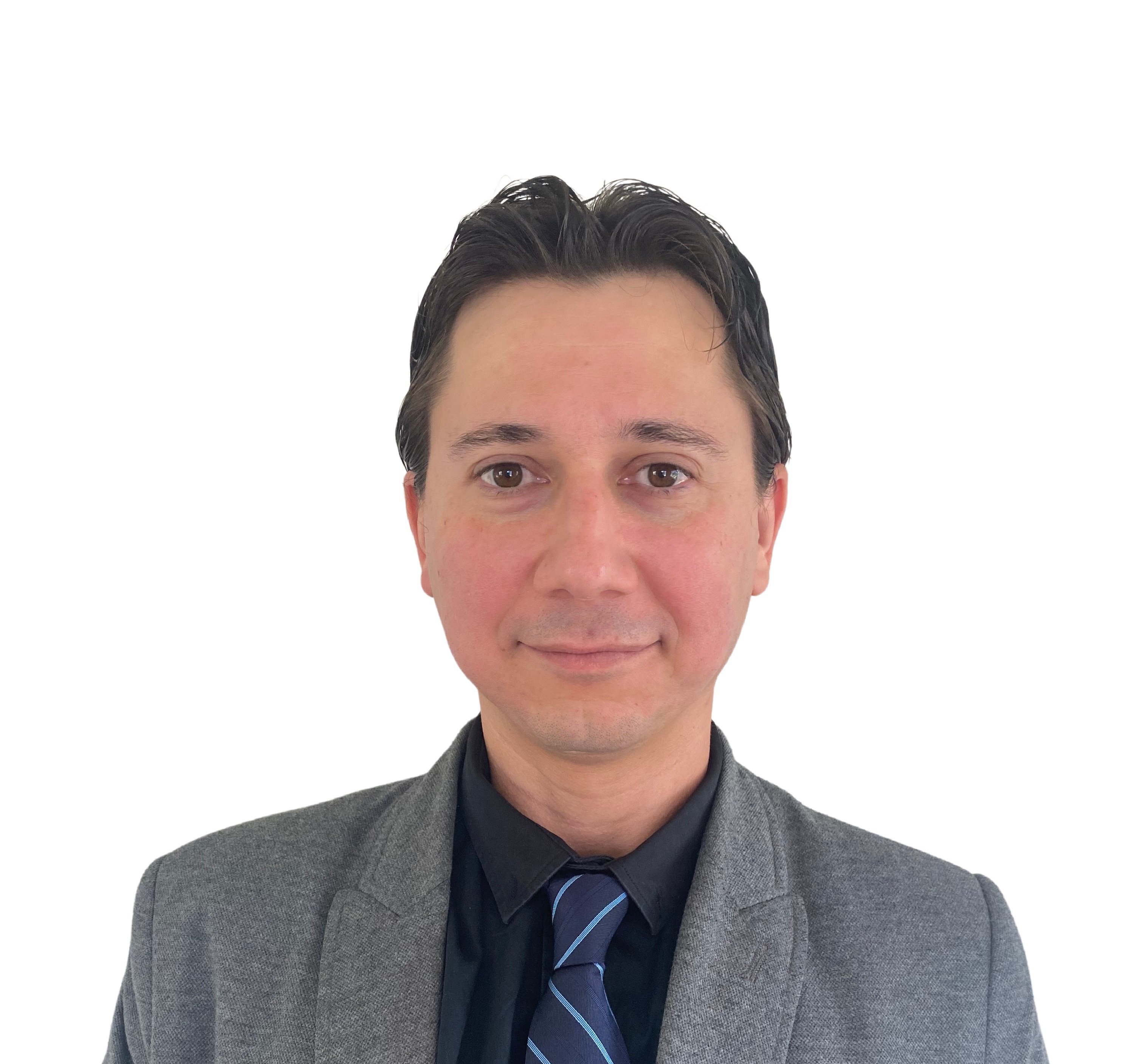