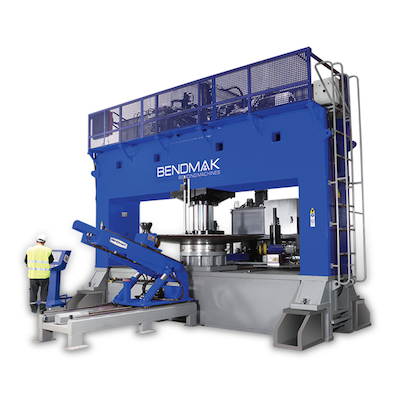
Posted By: Bendmak | Posted On: May 22, 2021 12:00:00 AM
Oxy-fuel or Plasma Cutting: Which Process is Best?
When deciding on a burning table (that's the general name for plasma and/or oxy fuel machines) the question arises as to how it should be equipped. Should you select Oxy-Fuel or Plasma, or even both? Which is best for your application and what’s the difference anyway?
It depends on a few factors, including the type of metal you’ll want to cut, the thickness of that metal, the tolerances you will be cutting too and the time/costy you're willing to invest in making these cuts. For thicker ferrous steel applications, an oxy-fuel is generally the better way to go. Other non ferrous materials like stainless and aluminum work much better under a plasma torch. However your understanding of the differences between the two cutting processes is crucial in knowing which to use, when to use it and what the benefits are.
Plasma Cutting
Plasma cutting uses an energized stream of Plasma which is a superheated, electrically ionized gas, which vaporizes and melts the material. Ideal applications for plasma cutting include steel, brass, copper and other conductive metals which yield under intense heat. Tolerances can be held as close as +/- 0.005” but are generally in the +/- 0.015” range.
Plasma cutting machinery are frequently not only found in steel fabrication shops but other applications too such as: automotive repair and restoration, industrial construction, and salvage and scrapping operations with many of these other applications using a hand held variant of the precision plasma found on Bendmak Machines.
With high speed, precision cuts and low cost, plasma cutting is suited to industrial applications where the material thickness is 2” or less and the tolerance variables acceptable..
Key benefits of Plasma Cutting include:
- The ability to cut any electrically conductive metals, including steel, stainless steel, aluminum and copper up to 2 inches thick.
- High speed cutting capabilities, generally 10X faster than Oxy-Fuel
- Precise cuts as the Plasma stream is much more controllable than Oxy-Fuel
- Minimal material distortion due to the high speed and small plasa stream
- Minimal slag providing a smoother cut then oxy-fuel.
- Greater ability to cut shaped metals, such as domes or tubes
- Lower cost with no preheating required, and greater ease of use
Oxy-Fuel Cutting
Oxy-Fuel cutting is a thermal cutting process that uses oxygen and fuel gas to create a flame. The flame is then positioned over the workp[ieces to preheat and then melt away a path of material. Gasses used in the Oxy-Fuel process can be acetylene, propane, propylene or natural gas, and are mixed with Oxygen to intensify the heat and effect resulting in an intensified burn.
Key Benefits of Oxy-Fuel cutting include:
- Thick metals yield easily under the intense heat of the Oxy-Fuel torch
- Multi Torch Applications are easily accomplished with Oxy-Fuel Systems and increase productivity while minimizing overall cutting time.
- Hardening of material surface through carbonization within the work zone.
- Operating Costs are lower as Oxy-Fuel does not need expensive consumables wuch as the swirl ring and nozzle found on Plasma systems.
How to Decide between Oxy-Fuel or Plasma?
Deciding between these two very capable processes does not have to be a difficult one as most machines are capable of supporting both technologies. And although cutting technology has its unique advantages, the most important factors to consider when choosing between plasma and oxy-fuel are the types of metal and the material thicknesses you will need to cut.
In general if you have the need to cut thicker metals, an oxy-fuel system makes the most sense for your operations. However, if you require precision cutting of not only steel, but stainless and aluminum too, the plasma cutter is your best choice.
Contact your team at BendmakUSA to see how the Bendmak BPM and BPM-T Series of Plasma and Oxy Fuel Cutting systems can add productivity and capability to your shop.
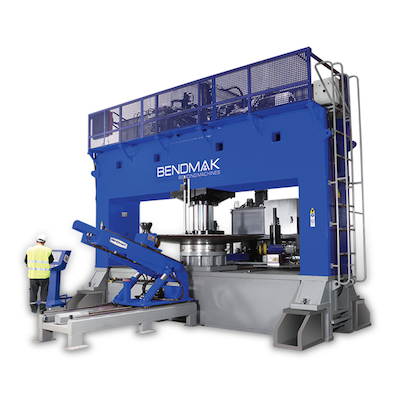