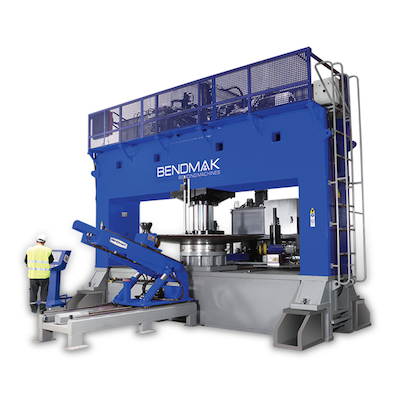
Posted By: Bendmak | Posted On: Jun 1, 2022 12:00:00 AM
10 Advantages of Plate Processing Machines that Integrate Multiple Processes
In plate processing, there are a variety of options to choose from. Milling, Plasma and Oxy fuel are just a few that can minimize the time you spend on your steel plate processing. But what are these processes and how does combining them affect the overall value of plate processing? In the next few paragraphs we will dig into what makes a steel plate processing machine the best value for a fabrication shop.
What is Milling?
Milling is a process whereby a rotating cutter is used to accurately machine out a contoured toolpath. In steel plate processing, it can also be used to drill holes, Mill larger holes or shapes and tap threaded features either with a fluted tap or with a thread milling cutter. While milling can be advantageous in plate processing for finish and accuracy, it may not be the best suited option for shape cutting.
What is Plasma Cutting?
In steel plate processing plasma cutting is probably the most efficient and profitable way to cut shapes. Utilizing a high energy jet stream of plasma combined with a highly pressurized jet stream of air the plasma literally vaporizes its way the steel plate creating contours easily and while the finish is relatively good, it may require some clean up afterwards. In a recent article titled Choosing the Right Plasma Cutting Table & Options to Get the Job Done Right we discuss Plasma cutting in much greater detail.
What is Oxy Fuel Cutting?
Oxy fuel Cutting is a very efficient way to process thicker steel plates. Usually utilized in material thickness of 2” (50mm) or greater oxy fuel combines flammable gasses such as Acetylene or Propane and Intensifies them with a high pressure jet of Oxygen creating a precise and powerful blow torch capable of cutting through even the thickest plate steel. Different at steel plate processing then the Plasma, the oxy fuel torch requires cleanup and secondary processing in almost every case. In a recent article we discussed Oxy-Fuel or Plasma Cutting: Which Process is Best? , which covers many aspects of the two processes.
The 10 Benefits of a Steel Plate Processing Machine that Integrates Milling, Drilling, Plasma & Oxy Fuel Capabilities:
Can Be Used on Different Types of Metals:
Not only can a plate processing machine quickly shape steels but they also can be quite efficient on Aluminum, Stainless and many other materials and grades of plate steel.
Meets Precise Specifications
Not only is the combination of the various processes efficient but an operator can choose between steel plate milling, plasma cutting or oxy fuel cutting to provide the greatest required accuracy.
Time Efficiency
Being efficient with time while processing plate steel is by far the most important factor. Having the capability to quickly choose and switch between oxy fuel, plasma and milling/drilling operations provides for the greatest efficiency in time.
Increased Productivity
When you are efficient with time in steel plate processing you become more productive. Producing more of the finished plate product is what a plate processing machine is all about. Drilling holes accurately milling features exactly and plasma or oxy fuel cutting the contours to size greatly increases productivity.
Minimal Material Distortion
One of the great benefits of steel processing on a plate processing machine is the ability to machine all the features in without having to “burn'' intricate details thereby minimizing the distortion caused by excessive processing heat.
High Cutting Accuracy
Another great benefit of the steel plate processing machine is the high accuracy obtained. Due to the capability of processing the entire plate in one setup the accray obtained is nearly identical to that of the positioning accuracy of the machine which is within just a few thousands of an inch.
Better Surface Finish
Choosing between processes also allows the operator of these plate processing systems to select the right process for the finish required. Milling will always provide the smoothest finish but is usually the slowest process whereby Plasma not be the best finish but provides the fastest processing speed. Only the designer or operator knows which process to employ and where.
Can Be Used in Various Types of Projects
Plate Processing machines can be used in a wide variety of applications including: Structural Fabricating, Truck & Trailer Frame, Rail/Car Applications , Crane components and so much more.
Can Cut Through Various Ranges of Metal Thickness
Plate processing machines can cut through materials as thin as Gage thicknesses to as thick as 12” (300mm) or more depending on the options the machine is equipped with. .
Can Cut Complex Shapes of Metal
Utilizing the Plasma and Oxy Fuel Cutting Capabilities of these plate processing machines, accurate and intricate contours can be designed and cut. Utilizing the milling capabilities allows pockets of details to also be accurately and efficiently cut.
Safety Features of Bendmak Plate Processing Machine
An important factor in any Plate Processing Machine is safety. Bendmak utilizes multiple layers of safety devices to protect both the operator and machine from damage. Safety doors, switched barriers and other safety features protect the operator whereas spindle overload alarms and collision avoidance software protects the machine from erroneous programmed collisions.
Shop Bendmak Plate Processing Systems
At BendmakUSA we offer a wide range of Plate Processing Machines for every shop’s budget and need.
- BEP - Heavy Duty Plate Drilling
- BEF - Standard Duty Plate Drilling Machines
- BPM-D Gantry - Combined Drilling & Oxy Fuel/Plasma Cutting Machines
- BECOP - Plate Positioning Combined Drilling & Oxy-Fuel/Plasma Cutting Machines
- BPM - Plasma Cutting Machines
Checkout our line of plate processing machines by clicking the link below or call us for more information at 833-BENDMAK (833-236-3625)
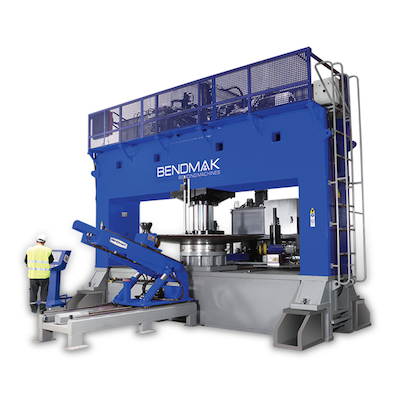