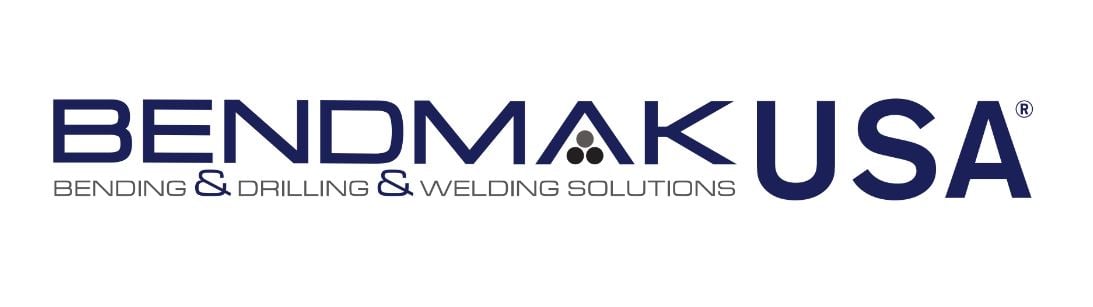
Posted By: BendmakUSA | Posted On: Mar 25, 2024 10:30:00 AM
Efficiency Comparison: Initial Pinch vs 4-Roll Plate Roll
Discover the key differences in efficiency between initial pinch and 4-roll plate rolls.
Understanding Initial Pinch Plate Rolls
Initial pinch plate rolls are a type of rolling machine commonly used for bending and shaping flat metal sheets into cones, tanks, pipe and other rounded parts. They operate by pinching the metal between two rolls, with the top roll typically fixed and the bottom roll moving up. This initial pinch action helps to grip the metal securely and prevent slipping. The adjusting roll, or bending roll, then moves diagonally up from a lower position to force the sheet upwards towards the top roll until the proper pre-bend has occurred. Then the roll is backed off, the material released and rotated repeating the process in order to prebend the opposite edge of the sheet before the rolling commences. These plate rolls are often preferred for smaller projects or when working with thinner materials.
Another advantage of initial pinch plate rolls is their versatility. They can be used for a wide range of applications, including bending, forming, and rolling various types of metal sheets. Whether you need to create curves, cylinders, or cones, an initial pinch plate roll can handle the task with ease although all done in a manual process.
Exploring 4-Roll Plate Rolls
4-Roll plate rolls, on the other hand, offer several advantages over initial pinch plate rolls. These machines feature four rolls instead of two, with two pinching rolls and two "bending" rolls on either side of the pinching rolls. The top roll has a fixed position, while the bottom roll moves up and down in order to pinch and release the material. Bothe side rolls are bending rolls and are used just like the initial pinch design, however this design does not require the sheet to be removed and rotated in order to prebend in each end of the sheet being formed. The design also allows for much easier automation systems to be added including CNC controls for rolling out of round materials such as buckets for tractors, oval fuel tanks and much more. This design allows for greater precision and control when rolling metal sheets.
One of the key advantages of 4-roll plate rolls is their ability to eliminate the need for pre-bending or pre-curving the metal in multiple setups. With an initial pinch plate roll, the metal must be pre-bent on each end of the sheet before it can be rolled. This extra step can be time-consuming, requires extra material handling and may result in inaccuracies. In contrast, 4-roll plate rolls can directly roll the metal without the need for removing the material for pre-bending, saving both time and effort.
Another advantage of 4-roll plate rolls is their ability to produce consistent and uniform bends. The four-roll design ensures that the metal is evenly distributed across the rolls, minimizing the risk of distortion or uneven bending. This is particularly beneficial when working with thicker or more rigid materials.
Additionally, 4-roll plate rolls offer improved efficiency and productivity. The simultaneous rotation of the top and bottom rolls allows for faster bending speeds and higher throughput. This can be especially advantageous in high-volume production environments where time is of the essence.
Efficiency Factors to Consider
When comparing the efficiency of initial pinch plate rolls and 4-roll plate rolls, there are several factors to consider. One of the main factors is the setup time required for each machine. Initial pinch plate rolls may require more time to set up\, pre-bend and adjust the rolls, especially when working with different thicknesses of metal. In contrast, 4-roll plate rolls often have a quicker setup time, as the side/bending rolls can be easily adjusted to accommodate different bending requirements.
Another factor to consider is the overall bending accuracy. While both types of plate rolls can achieve precise bends, 4-roll plate rolls are generally known for their superior accuracy. The four-roll design ensures that the metal is evenly distributed and bent symmetrically, resulting in more consistent and uniform bends. Additionally adding a CNC controller allows precise repeatability of the roll positions throughout the forming process.
Maintenance and upkeep should also be taken into account when evaluating efficiency. Initial pinch plate rolls may require more frequent maintenance, such as lubrication and adjustment of the pinch rolls. On the other hand, 4-roll plate rolls are often designed with self-lubricating bearings and low maintenance hydraulic systems, reducing the need for manual maintenance.
Lastly, the level of operator skill required can impact the efficiency of plate rolling operations. Initial pinch plate rolls, although easy to operate, require more experience to achieve optimum results. However, 4-roll plate rolls, especially those utilizing the CNC Controllers, require less skill and training to fully utilize their capabilities and achieve optimal efficiency.
Comparing Productivity Levels
When it comes to productivity, 4-roll plate rolls have a clear advantage over initial pinch plate rolls. The simultaneous rotation of the top and bottom rolls allows for faster bending speeds and increased throughput. This means that more metal can be rolled in less time, resulting in higher productivity levels.
Furthermore, the ability of 4-roll plate rolls to eliminate the need for separate set-ups for pre-bending or pre-curving the metal also contributes to their productivity. With initial pinch plate rolls, the extra step of pre-bending can slow down the overall production process. In contrast, 4-roll plate rolls can directly roll the metal, saving valuable time and increasing overall efficiency.
In high-volume production environments, the increased productivity of 4-roll plate rolls can significantly impact the bottom line. The ability to complete more bends in less time allows for faster order fulfillment and increased customer satisfaction.
Maximizing Efficiency in Plate Rolling
To maximize efficiency in plate rolling operations, it is important to choose the right type of plate roll for the specific application. For smaller projects or when working with thinner materials, an initial pinch plate roll may be a suitable choice. However, for larger projects or when precision and productivity are paramount, a 4-roll plate roll, with a CNC controller is often the preferred option.
Regular maintenance and inspection of the plate roll machine is also crucial for optimal efficiency. This includes lubricating moving parts, checking for wear and tear, keeping the hydraulic oil clean, ensuring the oil cooler is also kept clean and ensuring proper alignment of the rolls. By keeping the machine in good working condition, downtime can be minimized and productivity can be maximized.
Investing in operator training and skill development is another key factor in maximizing efficiency. Well-trained operators can make the most of the plate roll machine's capabilities and ensure accurate and consistent bends. Ongoing training and education can help operators stay up to date with the latest techniques and best practices in plate rolling.
Lastly, leveraging advanced technology and automation can further enhance efficiency in plate rolling operations. Many modern plate roll machines feature computer numerical control (CNC) systems, which allow for precise control over bending parameters and automate certain tasks. This not only improves efficiency but also reduces the risk of human error.
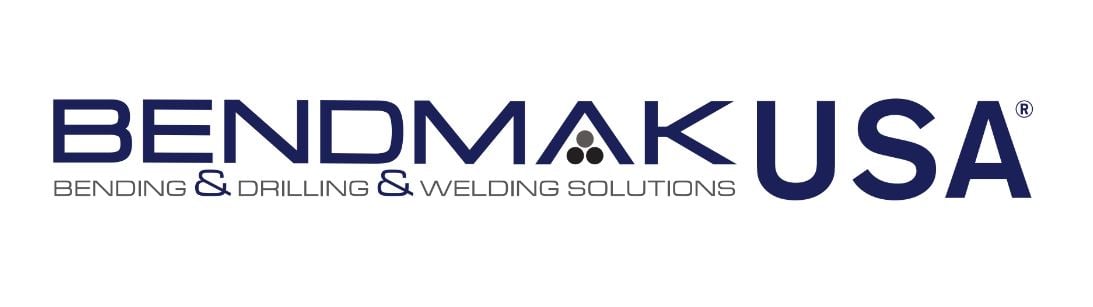