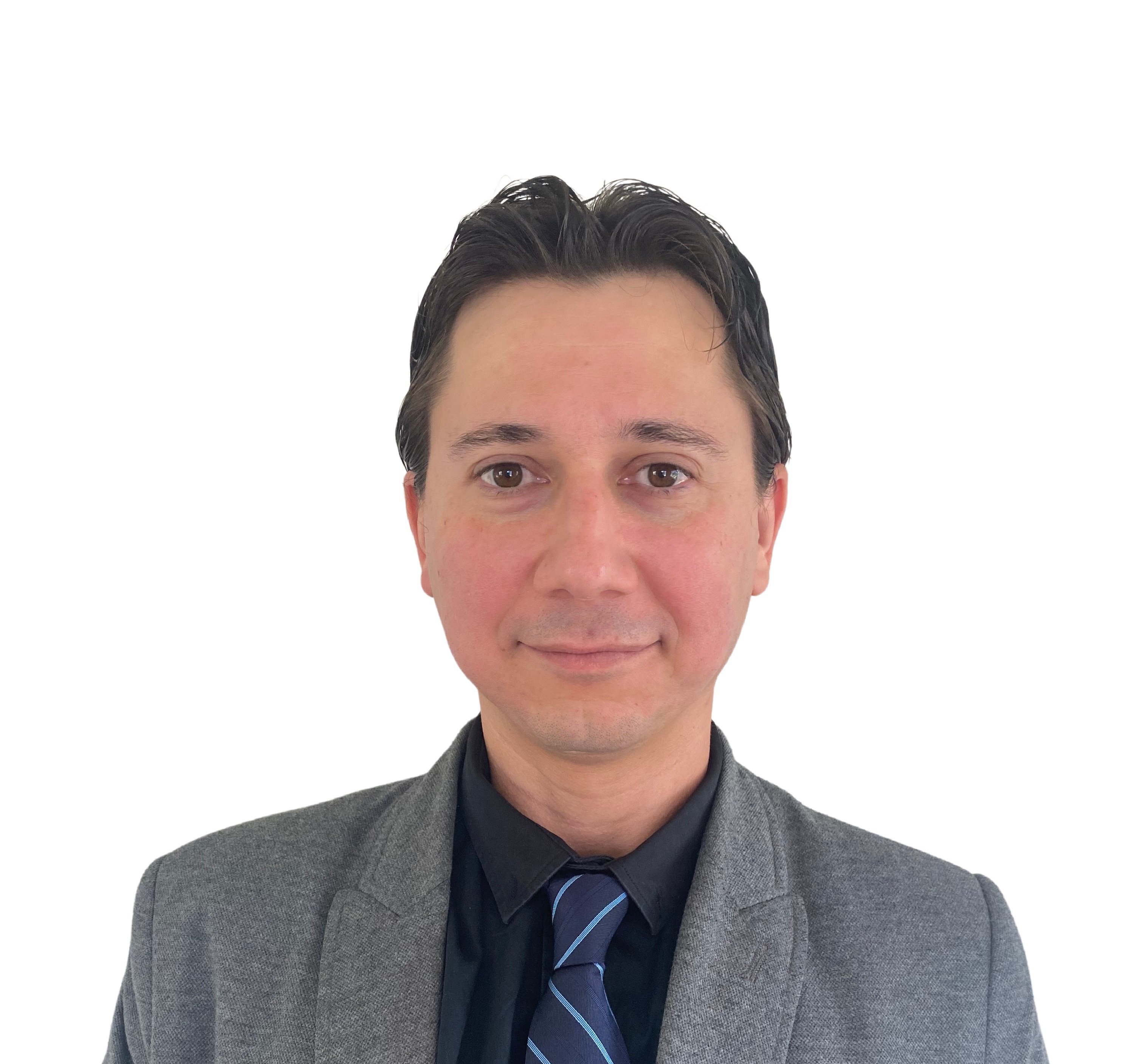
Posted By: Talip Tuzlular | Posted On: Jul 15, 2022 12:00:00 AM
What You Need to Know About Dishing and Flanging Machines
Pressure vessels, tanks on trucks, tank heads, silos or anything that has dished ends of different dimensions and types are produced with Dishing and Flanging Machines. The vast number of manufacturers need this type of metal formation on their parts in order to finalize their end products and thanks to the state of the art Dishing and Flanging Machines today, these manufacturing processes are simpler and more efficient than ever before. Check out the link to see what BednmakUSA has to offer: Dishing and Flanging Machinery .
There are various types of methods that are used to have dished ends but the ultimate goals are the same: dishing and flanging parts with the highest possible productivity and to maintain the producers’ competitiveness in the market.
Dishing and flanging processes are not the same so let’s dive into both and learn more about each one of them below.
What is Dishing?
Dishing refers to the process of pressing pre-cut flat material and forming them into typically conical shapes by manipulating and pressuring the material with a set of dies. Dishing presses come in various types and the larger the material radii get, the more difficult and challenging it gets to perform the dishing process. CNC dishing presses help operators perform the job easily and in most cases, one operator can get it done.
What is Flanging?
Once the dishing process is performed, the edges of the material need to be formed. This is necessary in order to properly weld the dished material onto a tank so that the pressure within the tank can be supported. During this process, it is highly possible that the material can get thinner so a good quality flanging machine would play a critical role here. It is also important to have the material not get thinner to avoid additional coating processes or using thicker materials. This saves manufacturers more money and time.
Benefits of a Dishing and Flanging Machine
There many benefits of using a dishing and flanging machine:
Automation
Today’s most dishing presses and flanging machines are equipped with high-tech systems and sophisticated CNC control units. This significantly increases the automation level and much less time is spent on production set up.
Precision
Less manual work and more automation through the technological advancements that are available today on most dishing and flanging machines lead to more precise end results. To prevent material from laminating, it is highly critical to have a machine with the correct capabilities and precise control over the flanging rolls. With a correct machine, even an inexperienced operator can perform the flanging with the least number of passes.
Maximum Efficiency
Efficiency is the natural result of an automated process that provides precise formed materials. A capable machine that can shape the rolls as precisely as possible increases the overall production efficiency, therefore helping the bottom line of the organizations.
What Makes Bendmak Dishing & Flanging Machines an Ideal Solution
Bendmak has one of the largest dishing and flanging machine selections in the world. The state of the art manufacturing facilities and processes are just some of the values that set Bendmak apart from its competitors. Through powerful partnerships with world-class technology companies and distribution network, Bendmak has proven to be one of the best manufacturers with its robust, well-built and supported dishing and flanging machines.
Check out our dishing presses and flanging machines on our website for more details or call us for more information at 833-BENDMAK (833-236-3625)
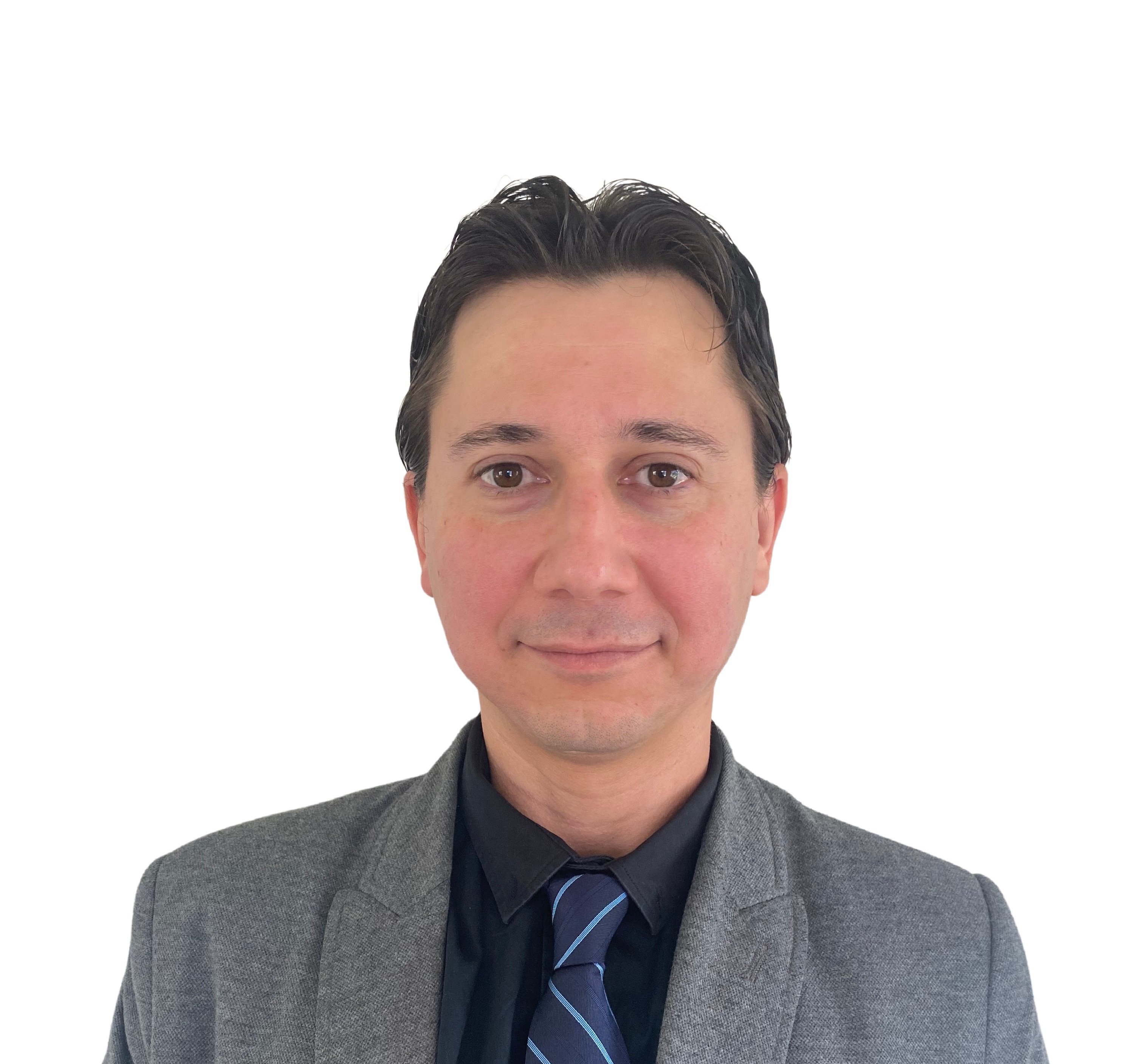