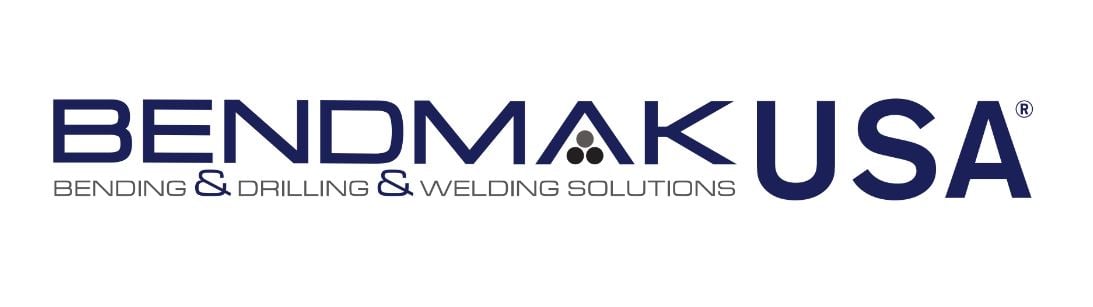
Posted By: BendmakUSA | Posted On: Mar 18, 2024 10:30:00 AM
Choosing the Right Tank Rolling System for Efficient Production
Discover the key factors to consider when selecting tank rolling equipment for optimal production efficiency.
Understanding the Importance of Tank Rolling Systems
Tank rolling systems play a crucial role in the production process for various industries. These systems are used to move and rotate tanks, allowing for efficient and effective welding & layout operations. Understanding the importance of tank rolling systems is essential in selecting the right equipment for your production needs.
One key benefit of tank rolling systems is their ability to handle heavy loads. Tanks can be extremely heavy and bulky, making them challenging to move and manipulate manually. Tank rolling systems, equipped with powerful motors and sturdy construction, can safely and efficiently handle the weight of tanks, reducing the risk of accidents and injuries.
Additionally, tank rolling systems provide precise control over the movement and rotation of tanks. This level of control is vital in ensuring accurate positioning during various stages of production, such as welding, painting, or assembly. By using a tank rolling system, manufacturers can achieve consistent and precise results, leading to improved product quality.
Furthermore, tank rolling systems offer flexibility in terms of tank size and shape. These systems can be customized to accommodate different tank dimensions, allowing manufacturers to work with a wide range of tank sizes. Whether you need to handle small tanks or large industrial containers, a tank rolling system can be designed to meet your specific requirements.
In summary, tank rolling systems are essential in modern manufacturing processes. They provide the necessary strength, control, and flexibility to handle tanks of all sizes, resulting in safer and more efficient production operations.
Factors to Consider When Choosing Tank Rolling Equipment
When selecting tank rolling equipment, there are several important factors to consider. These factors will help ensure that you choose the right system for your production needs and maximize the benefits it provides.
Firstly, you should consider the weight capacity of the tank rolling system. It is crucial to select a system that can handle the maximum weight of the tanks you will be working with. This will ensure safe and efficient operations without risking damage to the equipment or the tanks.
Secondly, consider the size and shape of the tanks you work with. Tank rolling systems should be designed to accommodate different tank dimensions, allowing for easy and secure positioning. Make sure to choose a system that can handle the specific tank sizes you commonly work with.
There are several types of tank rolling systems available such as the conventional style (CR) where two wheels are located on each stand. These are most suited for smaller tank sections in lighter gauge material. Another style is the Self Adjusting rolls (SAR), these offer the ability to handle much larger and heavier workpieces by supplying a pivoting yoke assembly on each end of the base unit with 2 heavy duty wheels on each yoke. A third style offers not only the flexibility to rotate the tank sections but also works in conjunction with a boom welding system to bring two tank shells together lifting and shifting them into proper position for seam welding these "Fit-Up Rolls" (SFU) offer the most flexibility for moving heavy workpieces into position.
Another important factor is the level of control provided by the tank rolling system. Look for systems that offer precise control over movement and rotation, allowing for accurate positioning during various production stages. This will ultimately contribute to improved product quality and overall efficiency.
Additionally, consider the durability and reliability of the tank rolling equipment. It is important to invest in a system that is built to last and can withstand the demands of your production environment. Look for equipment made from high-quality materials and backed by reputable manufacturers, such as Bendmak.
Lastly, take into account any additional features or customization options that may be beneficial for your specific production needs. This could include features like adjustable speed settings, remote control capabilities, or specialized attachments for specific tasks including boom welding systems for quality and accurate seam welding.
By considering these factors, you can confidently choose the right tank rolling equipment that will enhance your production efficiency and meet your unique requirements.
Cost-Benefit Analysis of Tank Rolling Systems
Conducting a cost-benefit analysis is crucial when considering the implementation of tank rolling systems in your production process. This analysis allows you to evaluate the potential financial impact and overall benefits of investing in this equipment.
Firstly, consider the initial investment cost of the tank rolling system. This includes the purchase price of the equipment as well as any additional installation or setup expenses. Compare this cost to the potential benefits and savings that the system can provide over its lifespan.
One of the main benefits of tank rolling systems is improved production efficiency. By using these systems, you can streamline your manufacturing processes, reduce manual labor, and increase productivity. This can result in significant time and cost savings in the long run.
Another important factor to consider is the potential reduction in workplace injuries and accidents. Tank rolling systems provide a safer alternative to manual handling of heavy tanks, minimizing the risk of injuries to workers. This can lead to reduced medical costs, insurance premiums, and potential legal liabilities.
Additionally, tank rolling systems can contribute to improved product quality. The precise control and positioning capabilities of these systems ensure consistent and accurate results, reducing the likelihood of defects or errors. This can lead to higher customer satisfaction, fewer product returns, and improved brand reputation.
Lastly, consider the potential for future scalability and versatility. Tank rolling systems can be customized and adapted to meet changing production needs and accommodate different tank sizes and lengths. This flexibility allows for future expansion or diversification of your product offerings without the need for significant equipment upgrades or replacements.
By conducting a thorough cost-benefit analysis, you can make an informed decision about investing in tank rolling systems. Consider both the upfront costs and the long-term benefits to determine the overall value and return on investment for your business.
Efficiency and Productivity Gains with the Right Tank Rolling System
Choosing the right tank rolling system can significantly improve efficiency and productivity in your production process. These systems offer several benefits that contribute to streamlined operations and increased output.
First and foremost, tank rolling systems eliminate the need for manual handling of tanks, reducing the reliance on manual labor and minimizing the risk of injuries. This allows your workforce to focus on other critical tasks and ensures a safer working environment.
Furthermore, tank rolling systems provide precise control over the movement and rotation of tanks. This level of control allows for accurate positioning during various stages of production, such as welding, painting, or assembly. This eliminates the need for time-consuming manual adjustment and ensures consistent results, ultimately leading to improved efficiency and reduced production time.
In addition, tank rolling systems can be integrated into automated production lines, further enhancing efficiency and productivity. These systems can seamlessly work alongside other automated equipment, allowing for continuous and uninterrupted manufacturing processes. This integration reduces downtime and maximizes output.
Moreover, tank rolling systems can be customized and tailored to your specific production needs. Whether you require systems for small-scale operations or large-scale industrial manufacturing, there are options available to meet your requirements. This flexibility allows for efficient production planning and resource allocation, optimizing overall productivity.
By selecting the right tank rolling system for your production needs, you can achieve significant efficiency and productivity gains. These systems enable safer operations, precise positioning, integration with automated processes, and customization for optimal performance. Invest in the right equipment and unlock the full potential of your production capabilities.
Selecting the Best Tank Rolling System for Your Production Needs
Selecting the best tank rolling system for your production needs requires careful consideration of various factors. By evaluating these factors, you can ensure that the chosen system aligns with your specific requirements and goals.
Firstly, assess the size and weight capacity of the tanks you will be working with. Choose a tank rolling system that can handle the maximum weight and size of your tanks to ensure safe and efficient operations.
Next, consider the specific functionalities and features you require. This could include adjustable speed settings, remote control capabilities, or specialized attachments for specific tasks. Determine the essential features that will enhance your production processes and select a system that offers them.
Additionally, evaluate the level of control provided by the tank rolling system. Look for systems that allow for precise and accurate positioning, ensuring consistent results and improved product quality.
Furthermore, consider the durability and reliability of the equipment. Investing in a high-quality system will minimize downtime and maintenance costs, ensuring uninterrupted production operations.
It is also important to take into account the future scalability and adaptability of the tank rolling system. Determine if the system can be easily customized or upgraded to meet potential changes in your production needs.
Lastly, research and compare different manufacturers and suppliers. Look for reputable companies with a track record of delivering reliable and high-quality tank rolling systems. Read customer reviews and testimonials to gain insights into the performance and customer satisfaction of the equipment.
By carefully considering these factors and conducting thorough research, you can confidently select the best tank rolling system for your production needs. Remember that investing in the right equipment is essential for achieving optimal efficiency and productivity.
The experts at BendmakUSA along with their team of distributors nationwide can help you select the right tank rolling system for your needs.
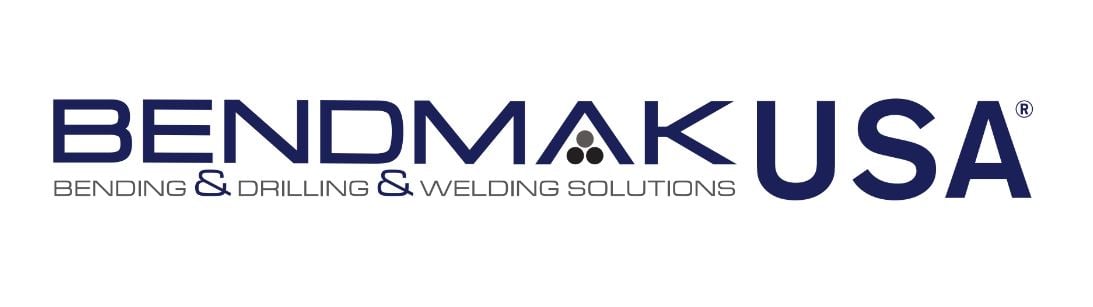